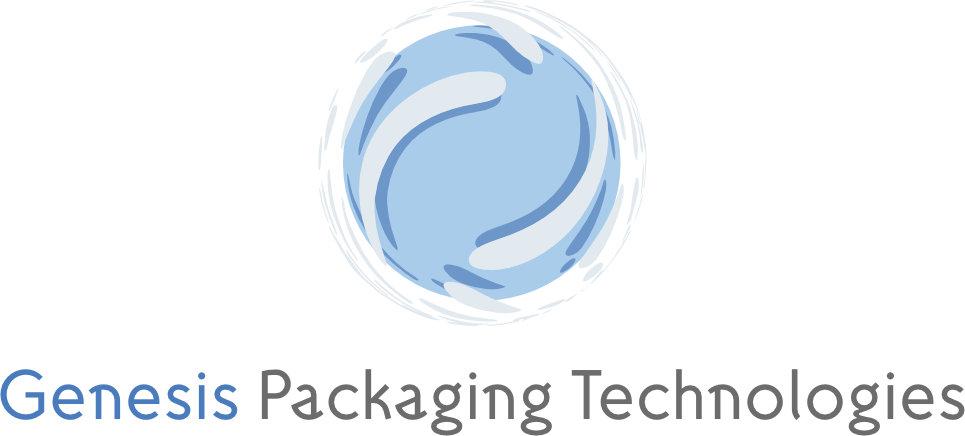
Aptus
The Aptus is a fully automated, servo driven, constant motion, rotary crimper. Ideal for mid to large production runs of time sensitive products such as lyophilized vaccines the Genesis Aptus is capable of sealing both large and small parenteral vials at up to 300 vials per minute.
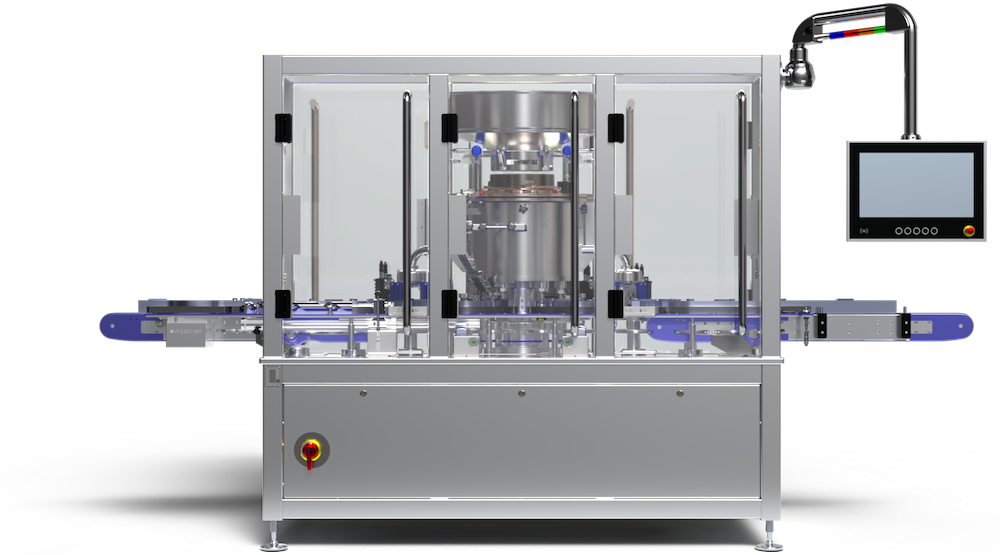
Advanced Crimping Process and Integrated Quality Assurance
Ensuring Seal Integrity
A stoppered vial remains the standard container closure system for parenteral drug products. However, true system integrity is only achieved when the rubber stopper is firmly compressed and secured by a properly crimped aluminum ferrule, eliminating potential leakage paths at the seal interface. Maintaining this seal integrity is critical for ensuring the sterility and stability of the drug product throughout its shelf life.
With the Aptus, Genesis Packaging Technologies takes precision crimping to a new level. Aptus allows for real-time setting and monitoring of the forces applied during the crimping process. By controlling and measuring elastomeric compression with high accuracy, the system minimizes variability in stopper compression, resulting in more consistent, high-quality seals batch after batch.
Designed for Modern Production Demands
The Aptus is purpose-built to meet the needs of mid- to large-scale production environments. Featuring state-of-the-art servo-driven controls, it offers precise adjustment of all critical motions—including the rotary motion of vial handling systems and the vertical actuation of the capping head. Despite its robust capabilities, the Aptus maintains a compact footprint, with a low overall height ideal for integration in facilities where space is limited. The cap hopper can be offset to the discharge side of the capping head to reduce particulate contamination and further decrease machine height.
Its fully modular design ensures easy scalability, enabling facilities to implement configurations that match their specific production requirements, whether for current operations or future expansion. Moreover, the Aptus has been developed to support compliance with European Annex 1 regulations for the manufacture of sterile medicinal products.
Gallery
3D Model
Total Vial Control and Modular Integration
At the core of the Aptus is a system architecture that keeps each vial under complete control throughout the entire crimping and inspection process. Additional starwheels integrated after the standard capper discharge star provide positions for various functional modules, including:
-
Marking and Reading
One starwheel positions the vial precisely for marking and vision inspection. The Aptus supports both inkjet and laser marking systems, combined with immediate Optical Character Recognition (OCR) verification to ensure marks are legible and accurate. Vials with non-conforming marks are automatically ejected from the line, ensuring only compliant products proceed downstream. -
Reject and Eject
A dedicated starwheel handles the removal of non-conforming vials identified during any inspection step, maintaining product quality and line efficiency.
Advanced Inspection Capabilities
Raised Stopper DetectionThe Aptus can be equipped with a highly sensitive vision system to detect raised or missing stoppers before vials enter the sealing stage. Dual color smart cameras provide redundant coverage and detailed inspection of stopper positioning and color, ensuring proper component use. Vials failing the set criteria are rejected automatically, preventing defective products from progressing further.
Post-Sealing InspectionTo guarantee seal integrity, the Aptus offers a post-sealing inspection station. As vials exit the sealing station, dual color cameras inspect each crimp for defects such as mis-crimps or missing seals. The system references programmable acceptance criteria stored in the PLC/PC controls, and any non-conforming vials are efficiently rejected via the eject starwheel. This robust inspection ensures that only properly sealed vials continue downstream for labeling and packaging.
Comprehensive Data and Compliance Support
When equipped with the optional Applied Force Monitor, the Aptus not only ensures precise force control during sealing but also enables comprehensive batch recordkeeping. This system can trace the cause of individual vial rejections, supporting both internal quality assurance processes and regulatory compliance requirements. Combined with vision systems placed prior to labeling, the Aptus offers a seamless path toward compliance with traceability and serialization regulations.
Flexibility to Fit Your Process
Genesis understands that no two production environments are identical. While the Aptus provides a sophisticated set of standard features, its modular, adaptable platform allows it to integrate seamlessly into diverse upstream and downstream processes. Whether your facility requires specialized marking, unique inspection systems, or custom handling configurations, the Aptus offers the flexibility to meet your precise needs—all while keeping every vial fully under control.
Aptus is more than just a crimping machine—it’s a complete solution for modern pharmaceutical packaging, delivering exceptional seal integrity, precise quality control, and modular flexibility for evolving production demands.
Features and Options
Recipes
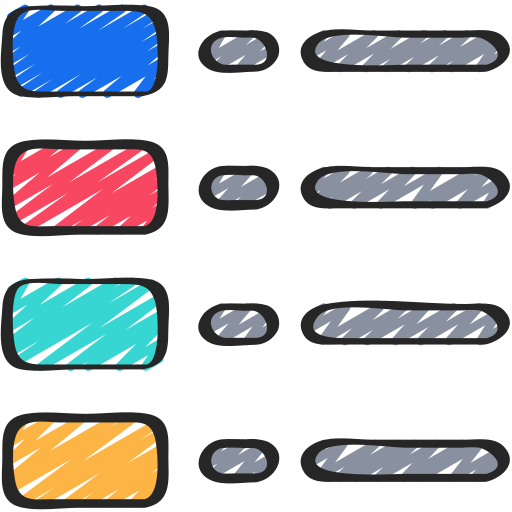
Recipes
Pre-programmed recipe buttons with optimized sealing settings for each package.
Networking
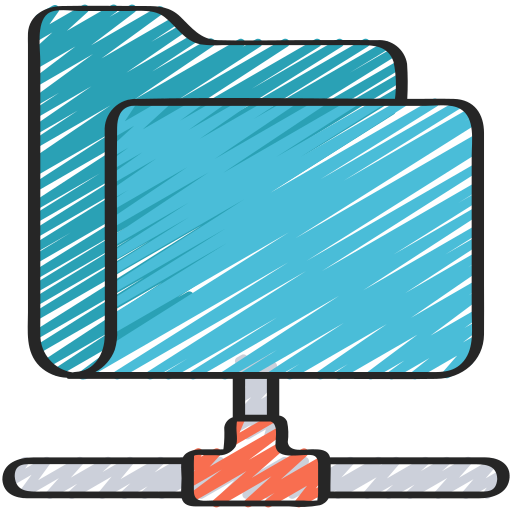
Networking
User/Active Directory & Network Integration.
Reporting
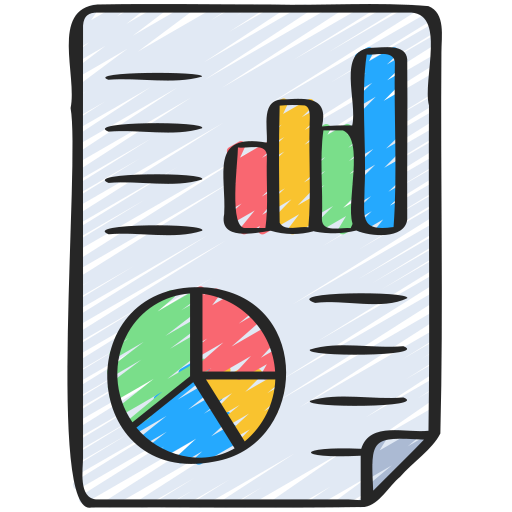
Reporting
Data Storage/Reports (21CFR11 capable).
Improve Your Crimping Process with Our Partners
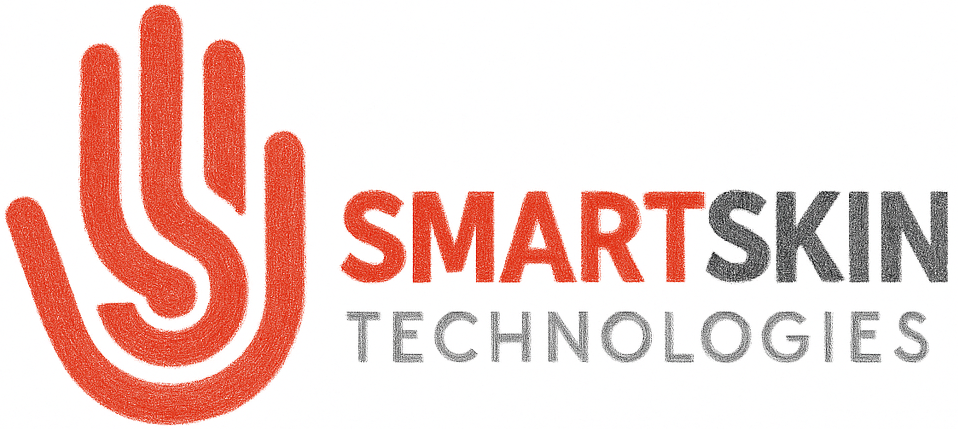
SmartSkin Technologies
Instantly Identify Capper Head Issues and Optimize Seal Quality with SmartSkin’s New Single & Multi-Drone Seal Assurance System
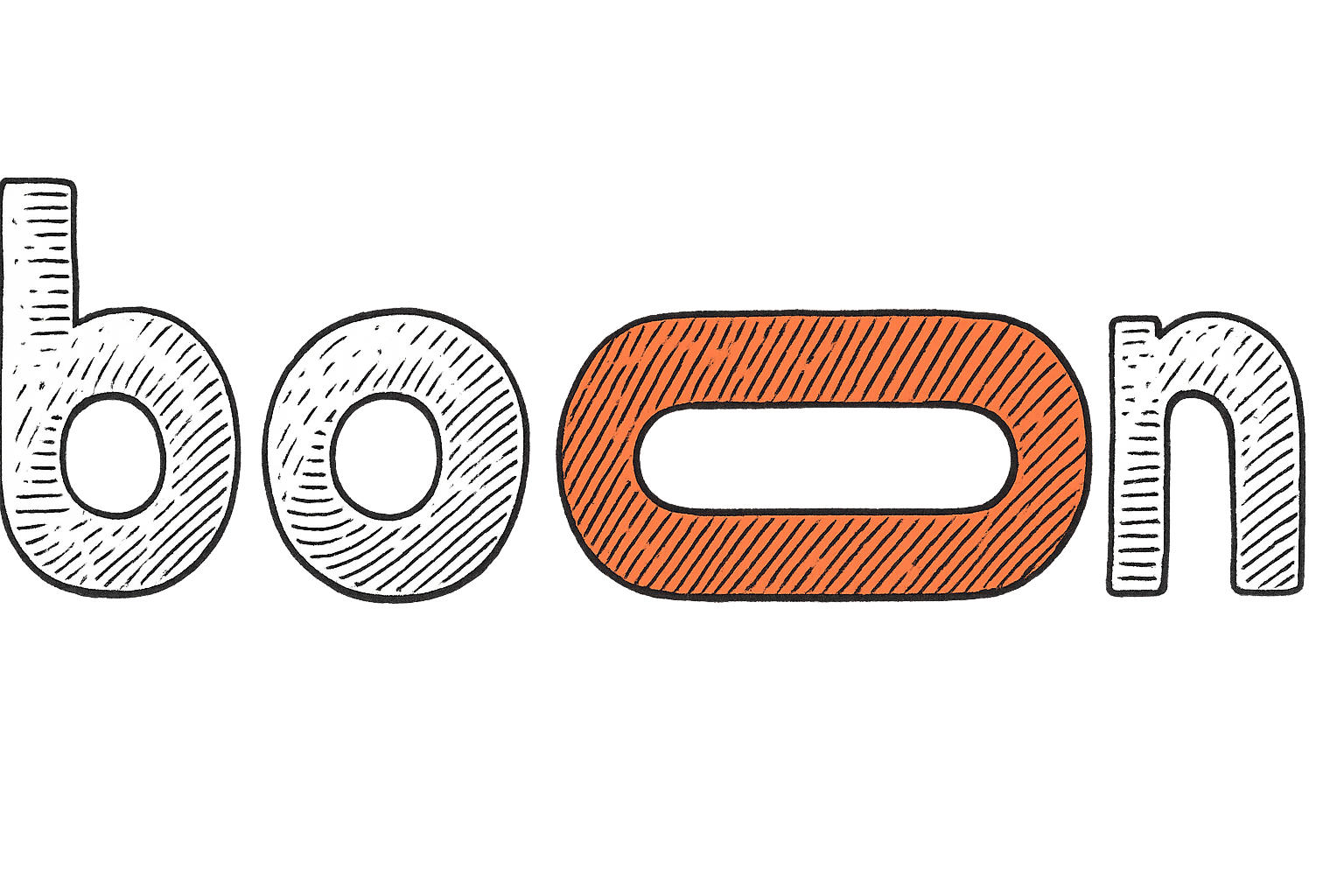
Advisum AI Powered by Boon Logic
AI Inspection Solution that has Been Proven to Optimize the Identification of True Rejects While Greatly Reducing the Number of False Rejects.
Specifications
Change Parts Cabinets
Heavy-Duty Rolling Cabinets for Organizing & Storing All Your Change Parts
Constructed from heavy-duty, powder-coated steel, these cabinets feature industrial casters for effortless mobility, allowing you to position them precisely where needed. Each drawer is custom-designed to organize and store the specific change parts for your capper. Available in two sizes to suit your space and storage requirements.
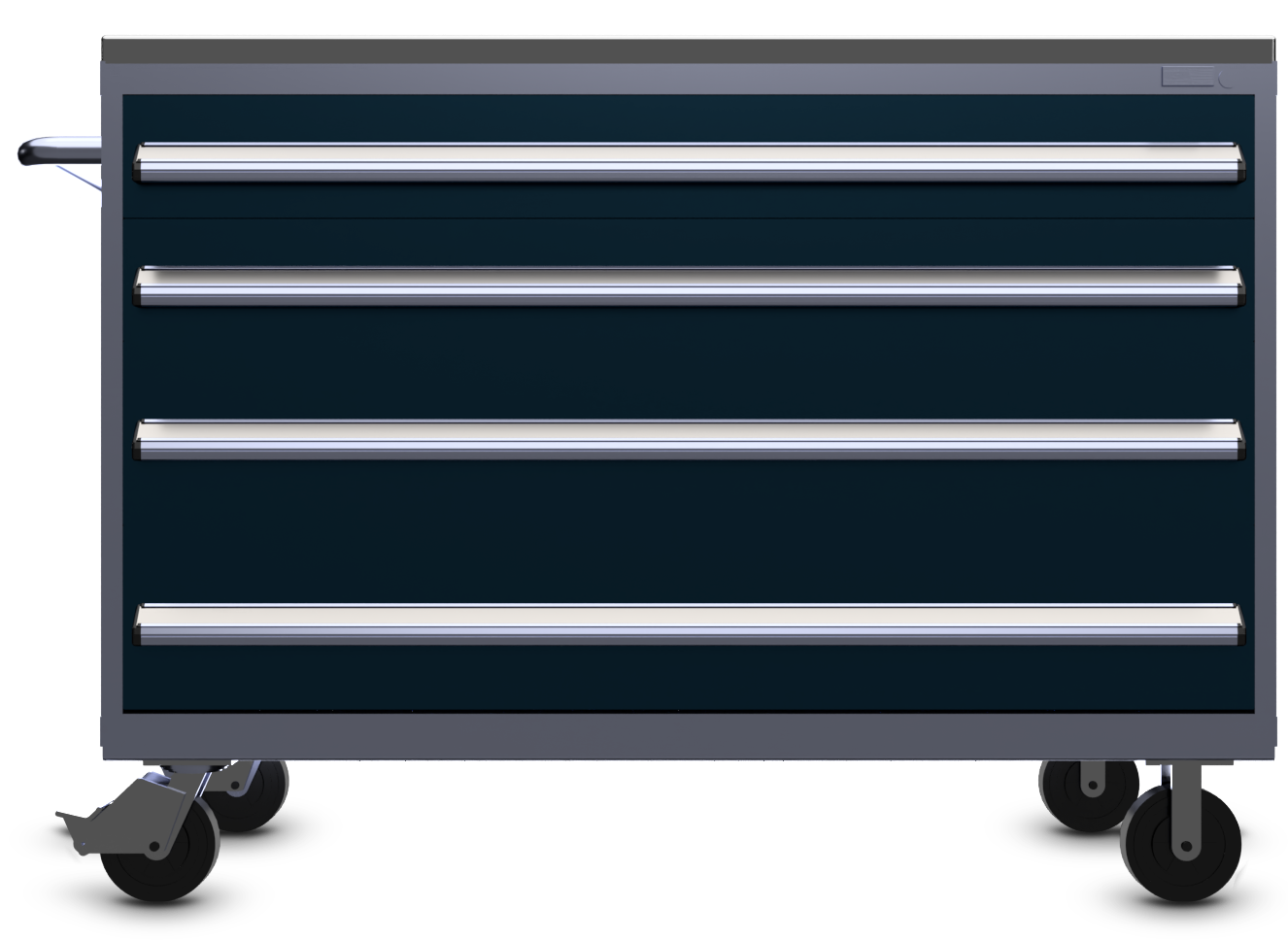